3D technology for aircraft value chain
highlights
- Aalberts surface technologies developed a HIP solution for Airbus Helicopters, enabling to begin production of latch shafts for the doors of a passenger aircraft
- the 3D-printed components are cheaper to produce and 45 percent lighter than traditional latch shafts
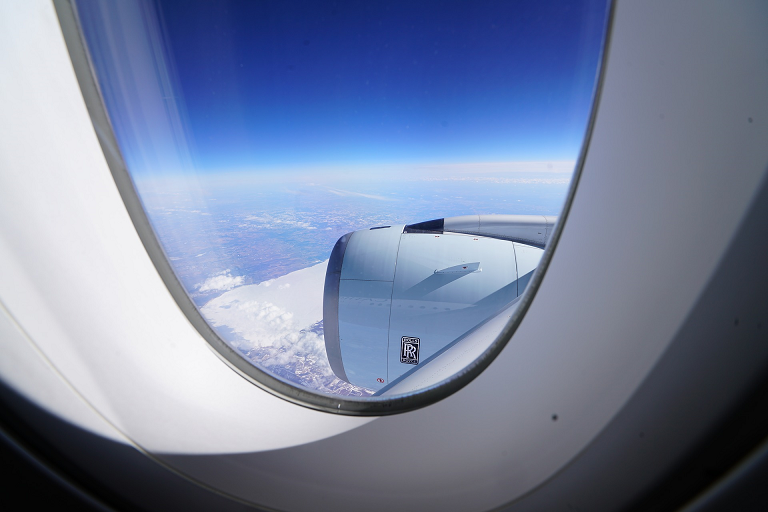
Because every kilogram counts in an aircraft, manufacturers are always on the lookout for parts that are lighter, more economical and less expensive.
Which is why Aalberts is proud to have developed a hot isostatic pressing solution (HIP) for Airbus Helicopters, enabling the company to begin serial production of latch shafts for the doors of the A350 XWB passenger aircraft. The latch shaft is produced by metal additive manufacturing, also known as 3D printing.
Not only are the 3D-printed components cheaper to produce, they are 45 percent lighter than traditional latch shafts. And because each A350 XWB has 16 latch shafts, switching production to metal additive manufacturing means a saving of over four kilos per aircraft.
Supported by strong cooperation across the company, Aalberts material technology successfully achieved all quality targets and project milestones, meaning we can focus on producing over 2,500 components per year for Airbus Helicopters, once manufacturing is fully operational.
The latch shaft is the first structural component that will be used in the air in an A350 aircraft and it's just the beginning of a great journey. Because we understand the printing process and can offer our customers unique post-processing technology in the field of surface, heat treatment and hot isostatic pressing, we are perfectly positioned to deliver metal additive manufacturing technology, all to the highest aerospace quality standards.
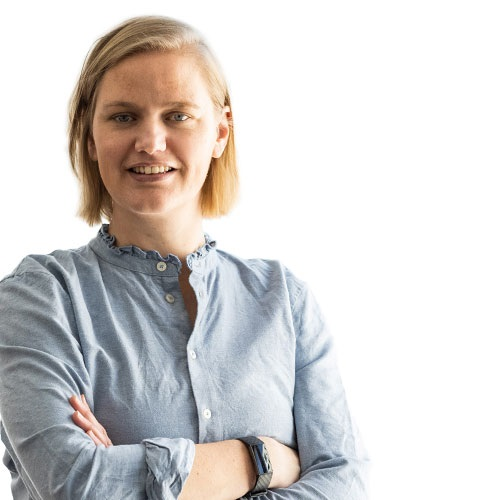