HIP and brazing, ultimate products
highlights
- One of the innovative treatment solutions from Aalberts surface technologies is hot isostatic pressing (HIP), especially valuable in the aerospace and automotive sectors
- the demand for such technologies grows, providing customers with greater choice and flexibility
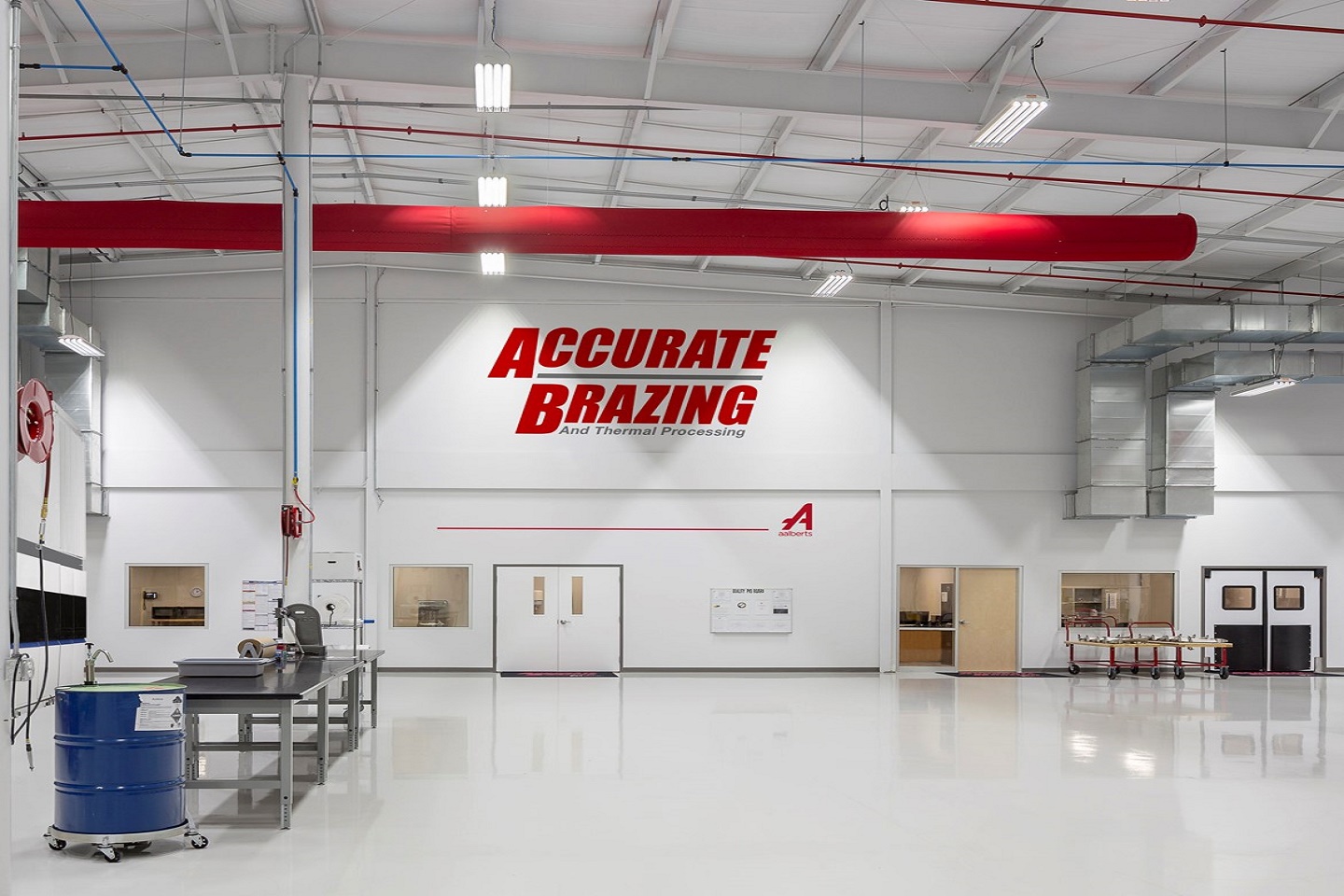
Aalberts surface technologies provides key customers, at both regional and global levels, with improved material characteristics for products across a wide range of industries. One of the innovative treatment solutions we offer is hot isostatic pressing (HIP), a process that enables us to provide customers with flexibility when designing and shaping components. This is especially valuable in the aerospace and automotive sectors, where custom-designed products are frequently required.
a flexible process
"HIP is the simultaneous application of heat and high pressure to materials," says Brent Davis, vice president at Accurate Brazing. "One of its real benefits is that it's effective with almost all materials – including metals, ceramics and plastics. We use our HIP process to provide customers with materials that have improved mechanical properties, such as greater fatigue strength and increased workability. The HIP process densifies, repairs and creates a clean uniform microstructure of the additive manufactured parts, while with powder metallurgy we can produce materials from metallic compositions that are difficult or impossible to forge or cast."
new frontiers
One industry where we apply our HIP process is the space sector, which thrives on innovation and technological progress. "For technology-driven organisations like Aalberts, such a fast-changing, high-margin environment leads to a raft of new opportunities," says Brent. "We applied HIP on a 3D-printed engine combustion chamber for Launcher, a New York-based rocket-development company, creating a more stable product that is far less likely to crack or be impacted by stress. We also applied the same technology in the aerospace sector, producing the latch shafts for the doors of Airbus's A350 XWB passenger aircraft."
We are investing in HIP as the demand for such technologies grows, providing customers with greater choice and flexibility. “In today’s manufacturing environment, service businesses like ours need to constantly improve our capabilities, especially when it comes to meeting the tight timelines of the aircraft and ground turbine industries," says Steven Francis, president of Accurate Brazing. "By focusing on technology and innovative solutions, we know we can help improve our customers’ world today, tomorrow and into the future."
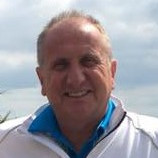