most sustainable expansion vessel
highlights
- Aalberts hydronic flow control has worked tirelessly on designing a Flexcon expansion vessel that has the smallest possible environmental footprint
- the unique aspects of the vessel is in the design and material of its membrane: made with better recyclable material with lower C02 footprint and longer lifetime expectancy
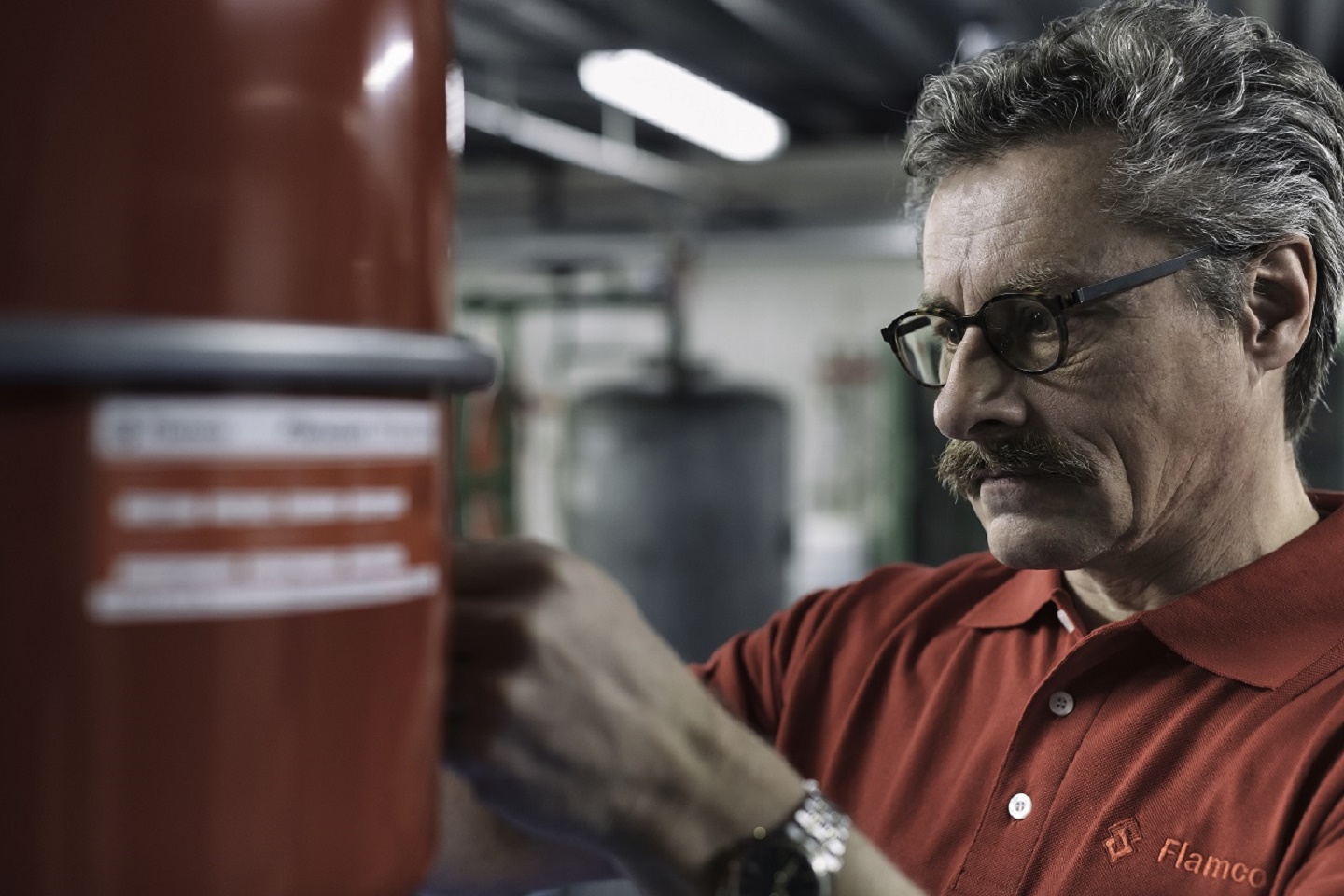
Expansion vessels are key components in many hydronic heating systems. They ensure the systems run safely and efficiently, and that water expansion goes unnoticed by a building’s occupants. But they need to be robust. And they need to ensure that the gas-tight membrane, which keeps the nitrogen in the vessel, remains tightly sealed. Yet the constant variations in temperature and pressure that occur within heating systems can lead to intense wear and tear, resulting ultimately in leakage and the need for the vessel to be replaced.
“On average, expansion vessels need to be replaced every 5-7 years,” explains Diem Kemper, head of product management at Aalberts hydronic flow control. “As well as being expensive, this is also unsustainable, with many materials in the vessels that will go to waste. Our engineers have been working tirelessly on designing a Flexcon expansion vessel that has the smallest possible environmental footprint, and lasts significantly longer than other vessels on the market.”
a unique product
Making this a reality meant focussing on the smallest of details: from reviewing the energy used for production, to cutting the cardboard and paper used for the user manual and in packaging. Yet while each detail was vital to making the product a success, the unique aspects of the vessel we produced is in the design and material of its membrane: it is made with better recyclable material than other membranes, it is material with lower C02 footprint, and it has a lifetime expectancy of at least twice that of rubber membranes. A truly sustainable proposition.
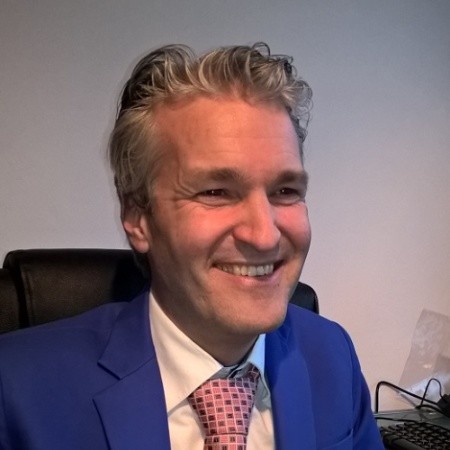